Comprehensive Guide to Laser Cutting Machine Maintenance
How to Extend the Life of Your Laser Cutting Machine?

Cici
date: 9th Dec 2024Trending and helpful laser knowledge for your success
Proper maintenance is crucial for ensuring the efficient operation and longevity of a laser cutting machine. This guide covers cleaning, lubrication, gas system care, and electrical maintenance, providing a detailed roadmap to keep your machine in peak condition.
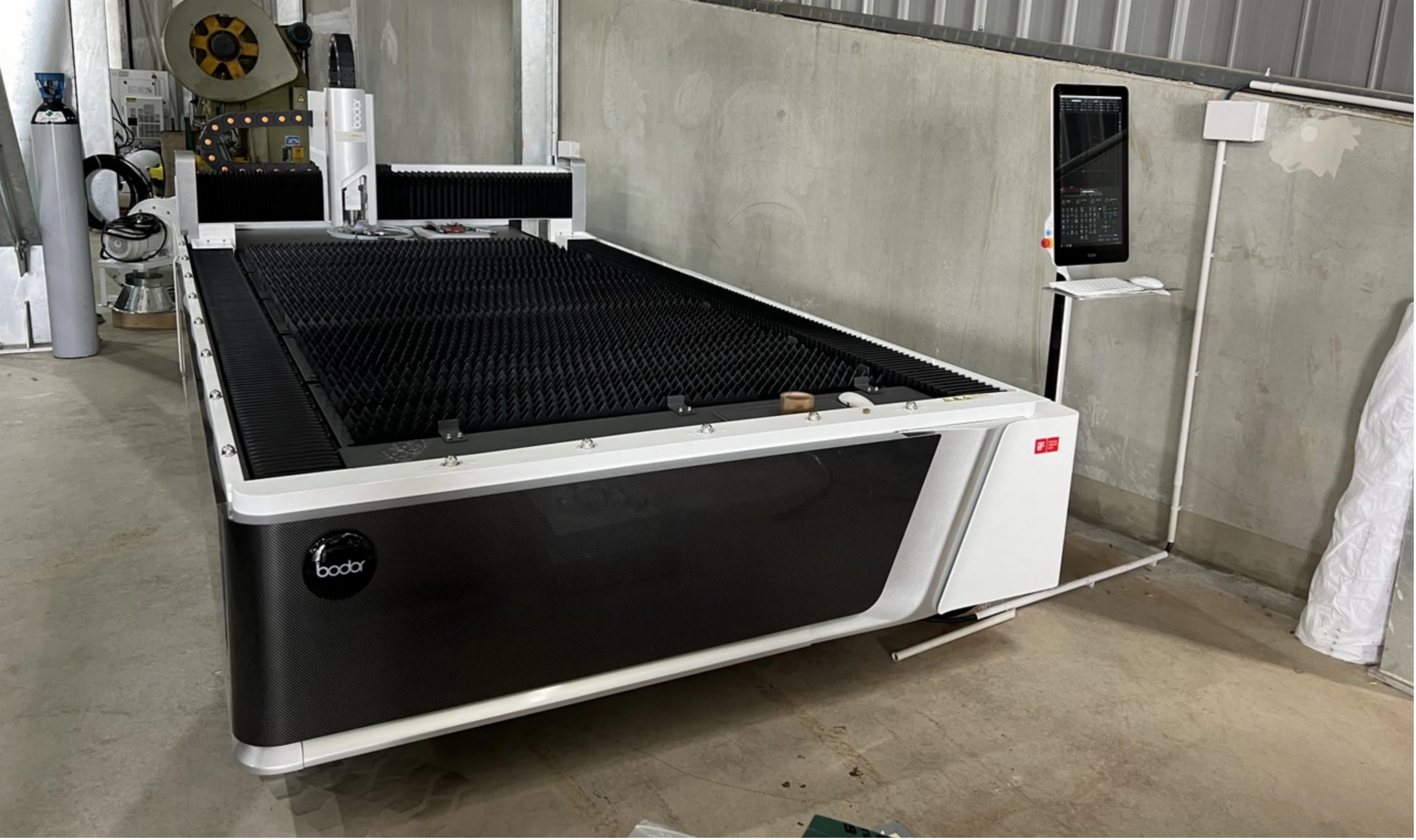
The Importance of Maintenance
A well-maintained laser cutting machine not only performs better but also prevents costly downtime and repairs. Whether it's cleaning the dust off components, lubricating moving parts, or replacing filters, consistent maintenance keeps your machine operating efficiently and extends its lifespan.
Below, we break down the tasks into daily, weekly, monthly, and annual schedules, so you can easily incorporate them into your routine.
I. Daily Maintenance
Daily tasks focus on cleaning and inspecting components to ensure stable operation:
X, Y-Axis Dustproof Cloth:Check and clean dust and slag.
Slag Collection Containers: Inspect and clean scrap vehicle containers.
X-Axis Protection Plate: Remove slag and dust.
Sheet Metal Appearance: Wipe external and internal surfaces to remove dust, grease, and dirt.
X-Direction Anti-Burning Plate: Regularly clean slag and dust.
Equipment Cleaning: Thoroughly clean both the exterior and interior of the equipment.
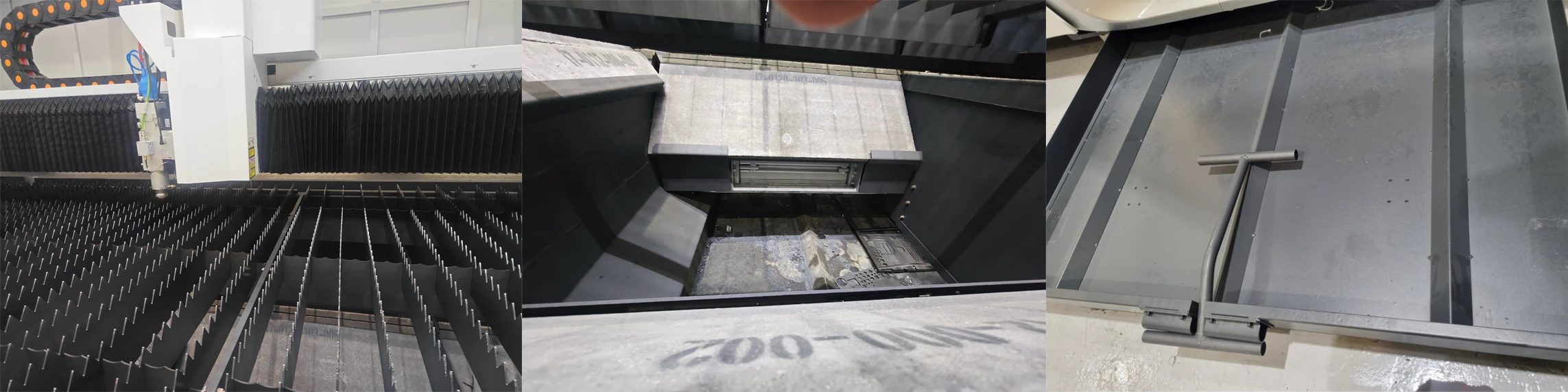
II.Scheduled Maintenance
Weekly Maintenance:
Head Shell Maintenance: Clean dust and lubricate the guide rail surface.
Monthly Maintenance:
Countertop Blade: Inspect and clean slag; replace if needed.
Self-Lubricating Container: Check, refuel, and clean regularly.
Bi-Monthly Maintenance:
Central Square Tube: Check and clean slags and dust in the air vent.
Water Cooling Machine: Clean the filter screen.
Safety Grating: Wipe and clean the surface.
Exhaust Duct: Periodically clean dust and slag.
Drive Chain:Clean, grease, and check for proper tension before tightening.
Quarterly Maintenance:
Self-Lubricating Container: Rinse thoroughly and replace the lubricating oil.
Oil Filter: Clean the filter element of the automatic lubrication system.
Annual Maintenance:
Filter Element: Replace the cutting air system filter element.
Chiller: Replace and clean the circulating cooling water.
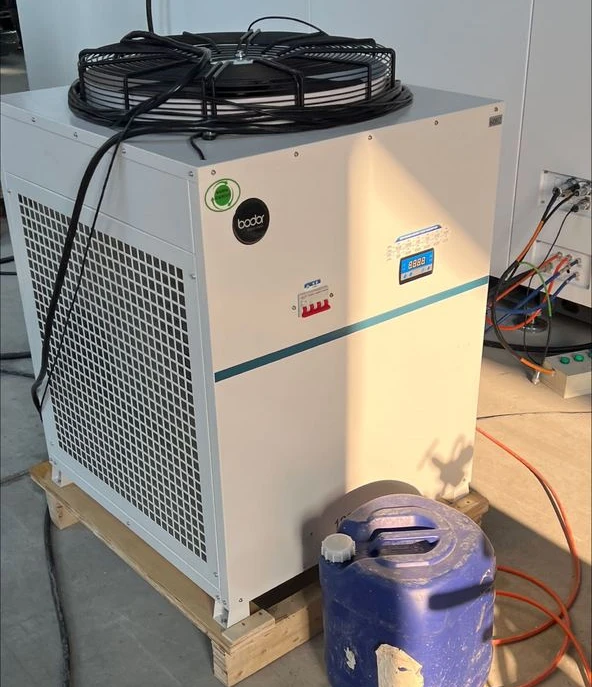
III. Lubrication Maintenance
Key Maintenance Points
1: X, Y-Axis Guide Rails
Interval: As configured by the system.
Tools: 32# guide oil.
Steps: Inspect lubricant levels and adjust as needed. Contact Bodor engineers if required.
2: Z-Axis Guide Rail and Lead Screw
Interval: Every 500 hours.
Tools: Cleaning cloth, grease gun, No. 1 lithium grease, 32# guide oil.
Steps: Remove hood components, clean linear guide rail, slide block, and ball screw, then apply grease.
3: X, Y-Axis Rack and Gear
Interval: Every 500 hours.
Tools: Cleaning cloth, alcohol, brush, 00# lithium grease.
Steps: Remove covers, clean the rack, gear, and linear guide, and apply lubricant.
4: Automatic Lubricant Pump
Interval: Refuel every 14 days; change oil every 6 months.
Tools: Cleaning cloth, funnel, refueling drum, 32# guide oil.
Steps: Clean the container, refill, and replace oil as needed. Ensure the container is clean inside and out.
5: Oil Filter
Interval: Every 1,000 hours.
Tools: Cleaning cloth, air gun.
Steps: Unscrew the filter base, clean the filter element with an air gun, reinstall, and tighten the base.
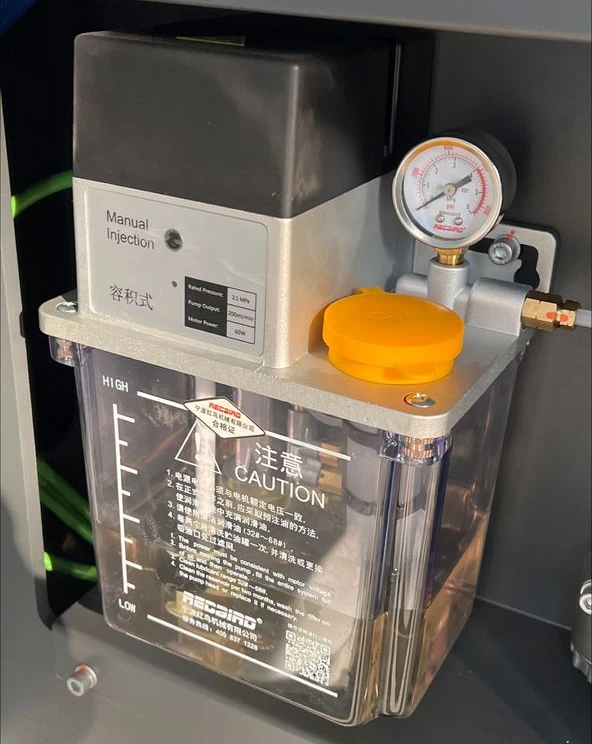
IV. Gas System Maintenance
Filter Element Replacement
Interval: Once a year.
Steps: Disassemble the filter, remove the old element, and replace it with a new one.
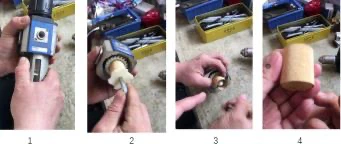
V.Electrical Maintenance
Every 1.5 Months:
Clean cabinet dust and inspect air filters. Replace damaged components.
Every 3 Months:
Inspect relays, contactors, and switches. Test control loops for proper function.
Annually:
Inspect and clean electrical components, tighten connections, check insulation, and calibrate sensors.
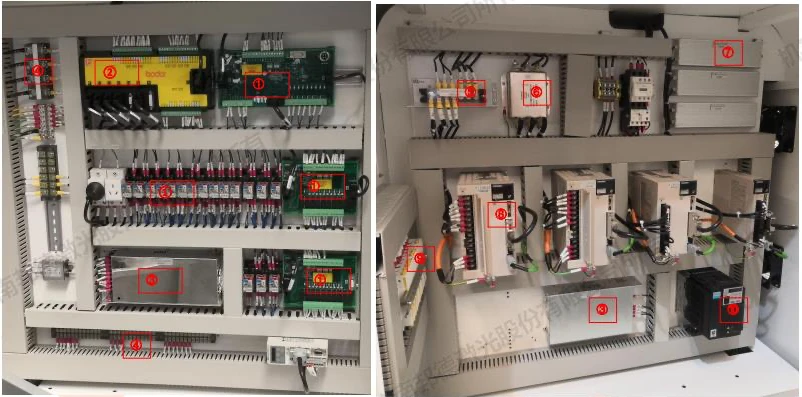
VI.Laser Cutting Machine Maintenance FAQ
Q1. Why is the laser output power decreasing?
Cause:Contaminated optical lenses, laser aging, or cooling system issues.
Solution: Change the optical lenses regularly, check the laser's performance, and ensure the coolant is clean and circulating properly.
Q2. What should I do if the cutting quality is poor?
Cause:Misaligned focus lens, improper cutting parameters, or clogged nozzles.
Solution: Adjust the focus lens, optimize cutting speed and power settings, and clean the nozzles routinely.
Learn common cutting defects and solutions
Q3. Why is the cooling system malfunctioning?
Cause: Insufficient coolant, clogged filters, or substandard water quality.
Solution: Refill or replace the coolant, clean or replace filters, and use purified water or specialized coolant.
Q4. What causes wear and tear on transmission components?
Cause: Insufficient lubrication or prolonged high-load operation.
Solution: Lubricate transmission components regularly and inspect gears, rails, and other critical parts for signs of wear.
Q5. Why does the machine frequently trigger alarms?
Cause: Sensor malfunctions, loose electrical connections, or user error.
Solution: Inspect sensors and electrical wiring, and follow the operational manual carefully.
Q6. What should I do if the cutting head collides with the workpiece?
Cause: Errors in programmed paths or sensitivity issues with the sensing system.
Solution: Optimize the programmed cutting paths and recalibrate the sensing system.
Q7. Why won't the machine start or operate properly?
Cause: Unstable power supply or control system software glitches.
Solution: Ensure stable power voltage.
Q8. What is the recommended environment for operating the machine?
Answer: A dry, dust-free environment with a stable power supply and controlled temperature to ensure optimal performance.
Q9. What are the benefits of regular maintenance?
Answer: Regular maintenance extends the machine’s lifespan, enhances production efficiency, ensures consistent cutting quality, and reduces downtime and repair costs.
By following these guidelines and addressing common issues proactively, you can maximize the performance and reliability of your laser cutting machine.
Have any further questions about maintaining your laser cutting machine?
Contact our expert team to learn more about professional maintenance tips and tailored solutions for keeping your equipment running at peak performance.
Contact Us Now
Let Bodor Laser help you get the most out of your machine!
Leave a comment
Your email address will not be published. Required fields are marked*