Plasma Cutting vs. 10kW+ High-power Laser Cutting Which One Is Optimal for Metal Processing?
As Industry 4.0 is revolutionizing the way companies manufacture and improve their products, farsighted manufacturers are already considering transferring to a more advanced production mode.

Fredy
Dec. 11, 2024Trending and helpful laser knowledge for your success
Overview
The metal fabrication sector, which serves as the backbone for manufacturing, construction, and various industries, has experienced tremendous technological progress. The rapid development of 10kW+ high-power laser cutting has become one of the primary focuses in this progress and is influencing the market share of the manufacturing industry where traditional processing methods including plasma take up.
Each metal cutting approach possesses unique merits and limitations. To make a wise investment, you need to consider the following key factors:
· What is your goal? - Whether upgrading from plasma to a high-power laser cutter or selecting one of them based on business needs, ensure it matches your productivity requirements.
· What are your cutting requirements? - Your chosen machine should be able to process your specific materials, accommodate thickness, and deliver quality cuts.
· What’s your budget? - Don’t just consider the initial cost; think about ongoing operational expenses for long-term savings.
· Does your choice align with your plan? - With different equipment lifespans and environmental standards, your solution should support your long-term objectives.
Without further ado, let’s find the answers to all your questions in this article, as well as a personalized consultation service to help you choose the best option for your business.
Table of Contents
· 1. What is plasma cutting?
· 2. What is 10kW+ high-power laser cutting?
· 3. What are the main differences between plasma and 10kW+ laser?
· 3.1 Speed
· 3.2 Thickness
· 3.3 Precision
· 3.4 Cut Quality
· 3.5 Bevel Cutting
· 3.6 Cost Analysis
· 3.7 Maintenance
· 4. Make the Smart Decision
1.What is plasma cutting?
Plasma cutting is a method for cutting electrically conductive materials, especially metals. The process uses ionized gas or plasma, which generates high temperatures that melt the metal, allowing the accelerated stream to eliminate the molten material and create cuts.
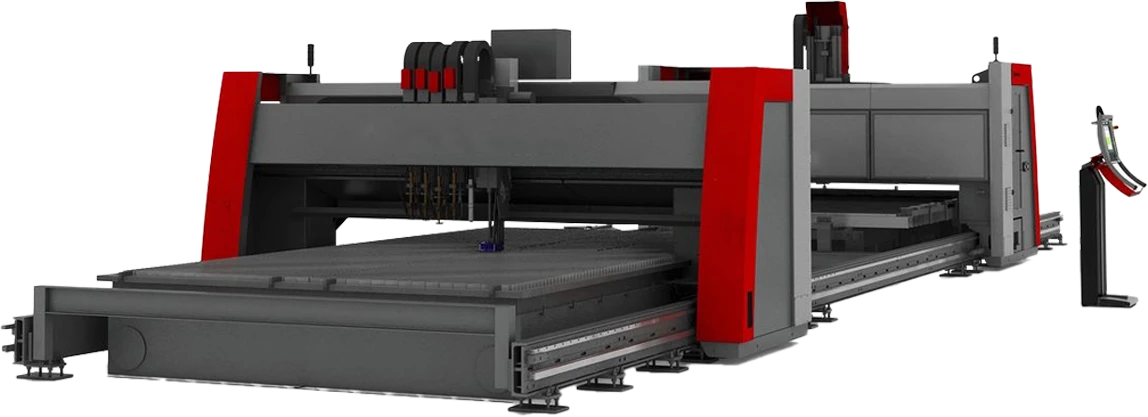
2.What is 10kW+ high-power laser cutting?
10kW+ high-power laser cutting is a technologically advanced procedure that utilizes fiber lasers of extreme power, typically ranging from 10kW to 60kW, to precisely incise a diverse array of materials. The intense laser beam is concentrated onto the material intended for cutting, inducing a rapid, localized elevation of temperature, consequently melting the material. The molten material is then extricated using a coaxial gas jet, producing a narrow and clean cut or kerf in the material.
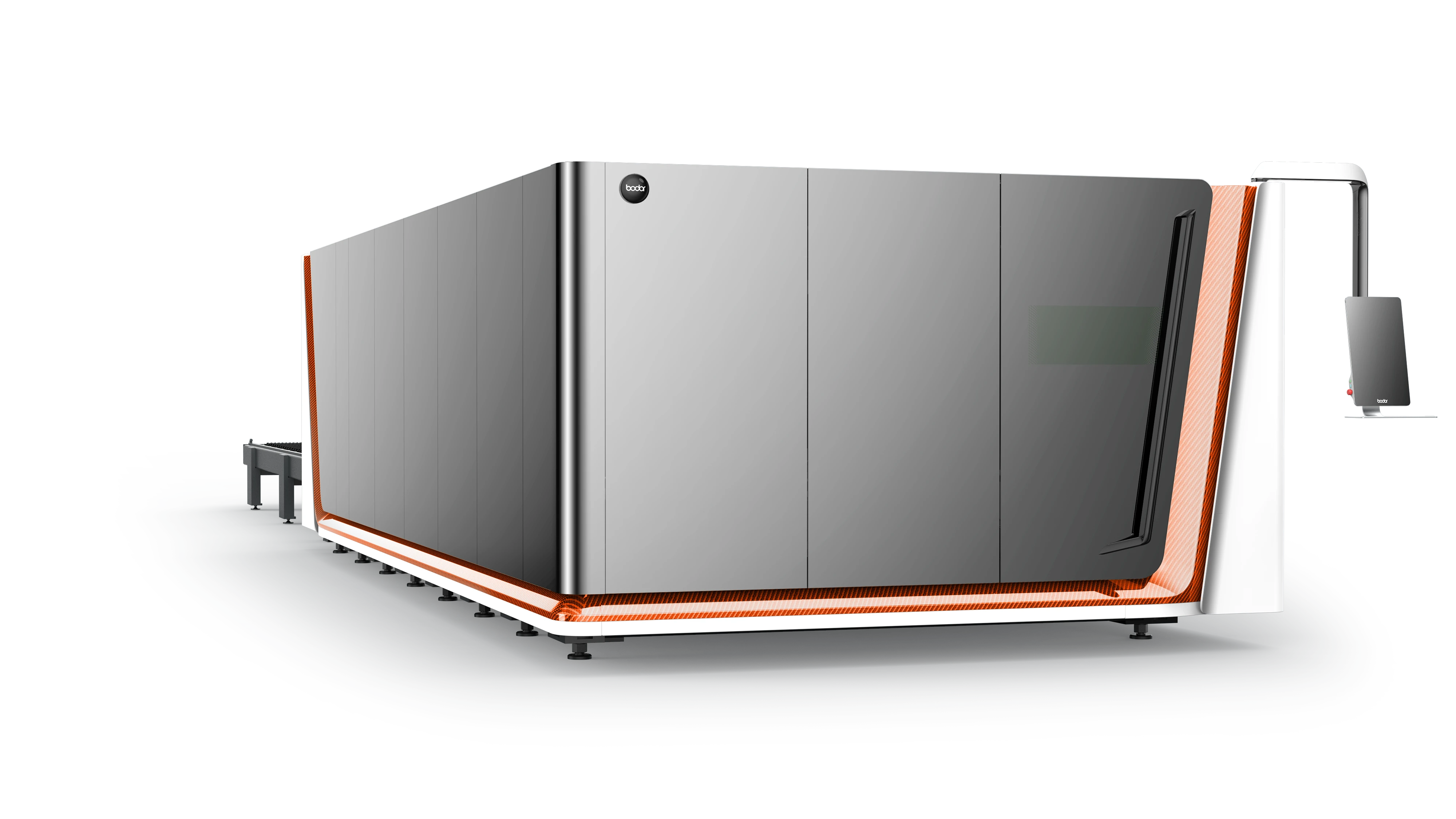
Bodor Laser Cutting Machine P Series(with protective cover)
3.What are the main differences between plasma and 10kW+ laser?
For manufacturers, cutting speed is one of the crucial factors that must be seriously considered. Compared to plasma cutting, 10kW+ high-power laser cutting offers significant advantages in terms of speed, achieving cutting speed up to 3 times faster.
This increase in speed can lead to higher earnings, enabling companies to swiftly fulfilling high demand and urgent orders. Additionally, it reduces per-unit costs, increasing higher potential profit margins, facilitating business reinvestment, and making companies able to recoup laser machine costs within 3 months at the earliest. Moreover, expedited processing allows for quicker product completion and delivery, boosting customer satisfaction.
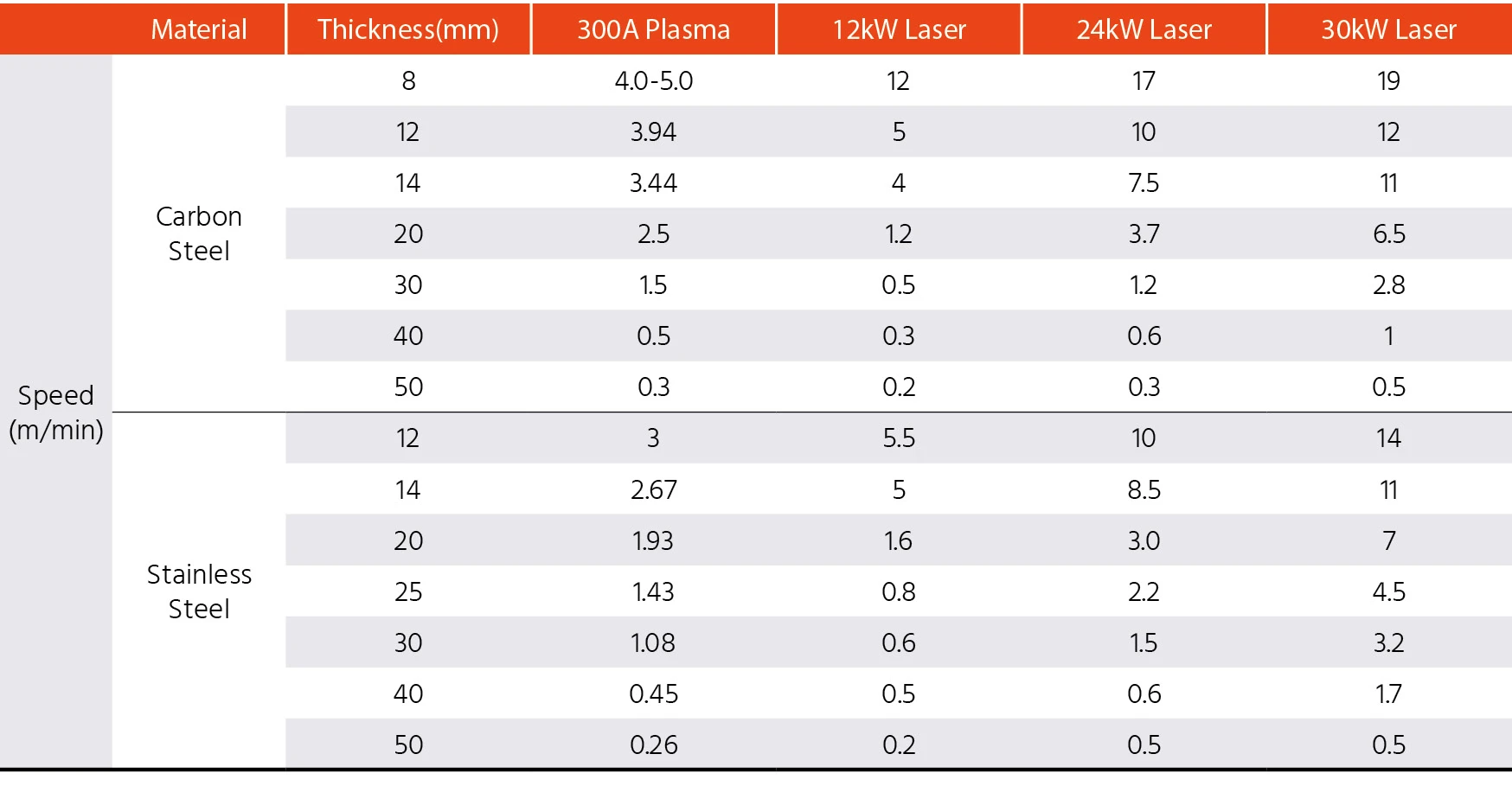
For a practical example, consider a company that provides metal cutting services using a Bodor P series 12kW laser cutting machine to process 14mm carbon steel, and operating it 10 hours per day, 25 days per month. By utilizing laser cutting technology, this company can process approximately an additional 9,000 meters of carbon steel per month compared with a plasma cutter.
· 3.2 Thickness
Many manufacturers persist in the belief that laser technology underperforms in the domain of thick plate cutting, particularly when compared with plasma-based alternatives. This concept, however, has been significantly challenged by the advancements made in the arena of 10kW+ high-power laser cutting machines.
Both plasma and high-power laser cutters have the ability to process thick metal plates. Remarkably, high-power laser devices can handle materials with a thickness of 60mm or greater, without compromising on operational speed, precision, and quality. Consequently, final outputs exhibit smooth edges and refined craftsmanship even when thicker materials are employed - a feat not attainable by plasma counterparts.
· 3.3 Precision
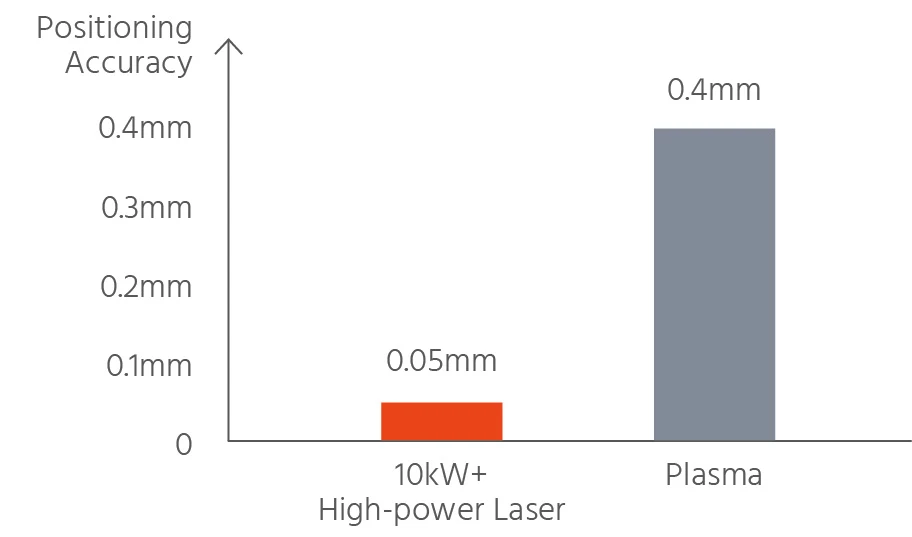
In terms of precision, 10kW+ high-power laser cutting offers unparalleled precision. It uses a high-density laser beam for cutting, allowing for an ideal positioning accuracy of 0.05mm. This is much more precise than plasma cutting, which only offers a positioning accuracy of 0.4mm.
The impact of this 0.35mm difference is significant due to the following reasons:
1.It minimizes roughness, ensuring the production of clean and sharp edges.
2.High precision enables the processing of intricate designs and complex shapes.
3.Precise cutting reduces the need for supplementary finishing processes, yielding high-quality results.
4.High precision guarantees consistent and reproducible outcomes, fostering uniformity in the finished products.
5.Achieving precise cuts reduces the requirement for rework, resulting in time and resource savings.
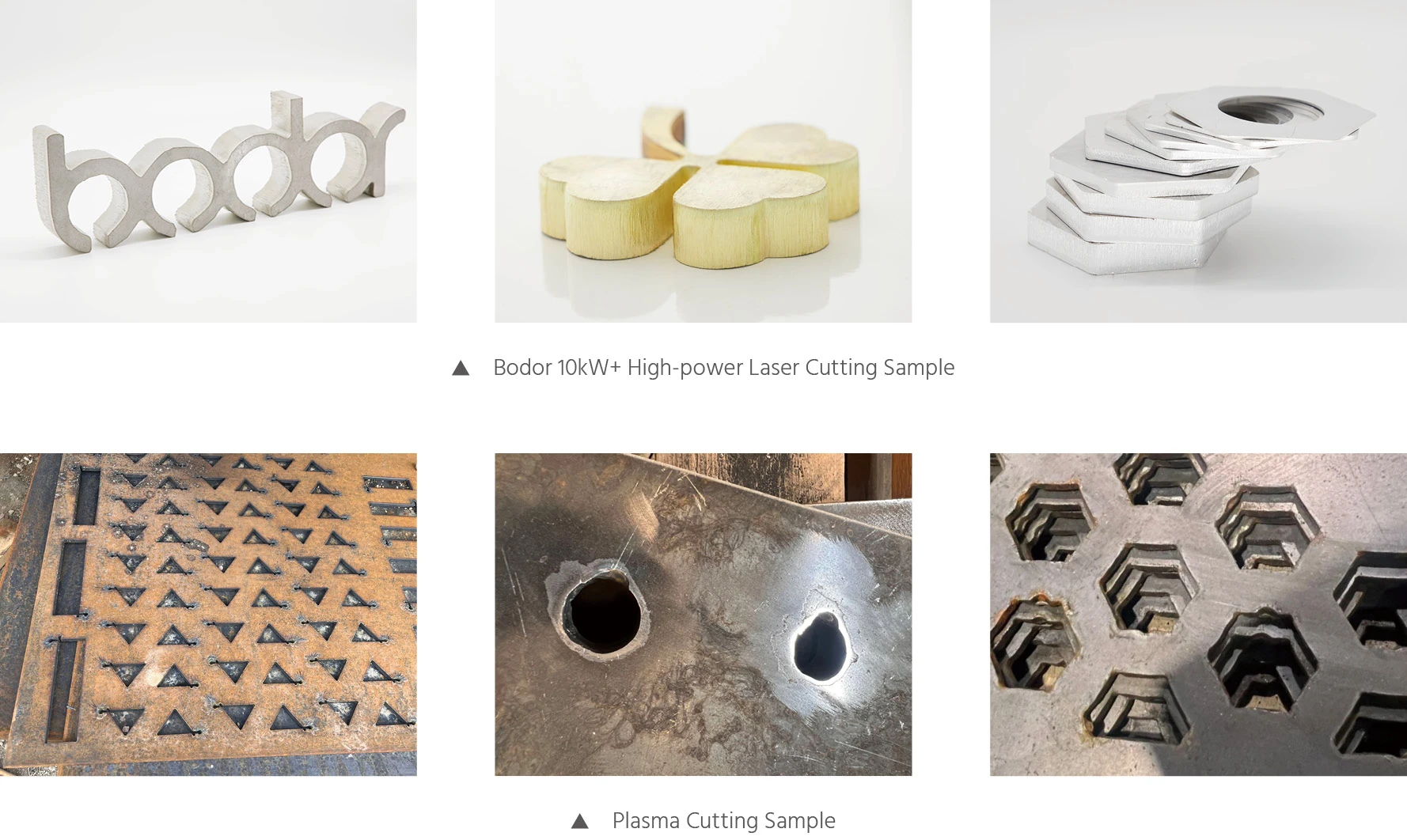
· 3.4 Cut Quality
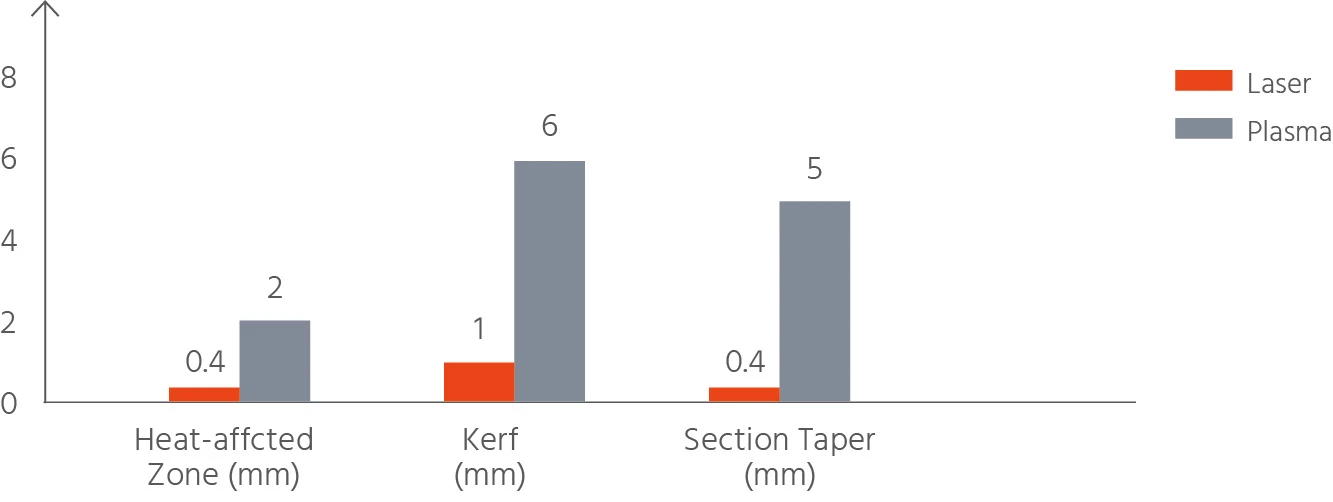
Heat-affected Zone
The plasma cutting process generates a sizable heat-affected zone, typically between 0.5 and 2.0mm, and this substantial thermal impact can lead to metal distortion. Conversely, laser cutting keeps the heat-affected zone restricted to a minimal 0.1-0.4mm so that materials experience minimal deformation, yielding smooth edges and surfaces devoid of slag formation and significantly enhancing the quality of materials.
Kerf
Plasma cutting, due to the wider kerf of 6 mm it produces, is a less-than-ideal option for high-precision applications or complex designs. Moreover, plasma cutting often results in slag, dross, and rough edges, which generally require subsequent grinding and burnishing to ensure surfaces and edges are adequately smooth for later assembly. However, the kerf high-power laser produces is only 1mm, and the surface and edge of metal parts processed by laser cutting are usually smooth, burr-free, and scratch-free, reducing friction, wear, and corrosion.
Taper
Plasma users often find that the finished products are with a taper that has two parallel edges with exaggerated angularity and require grinding.
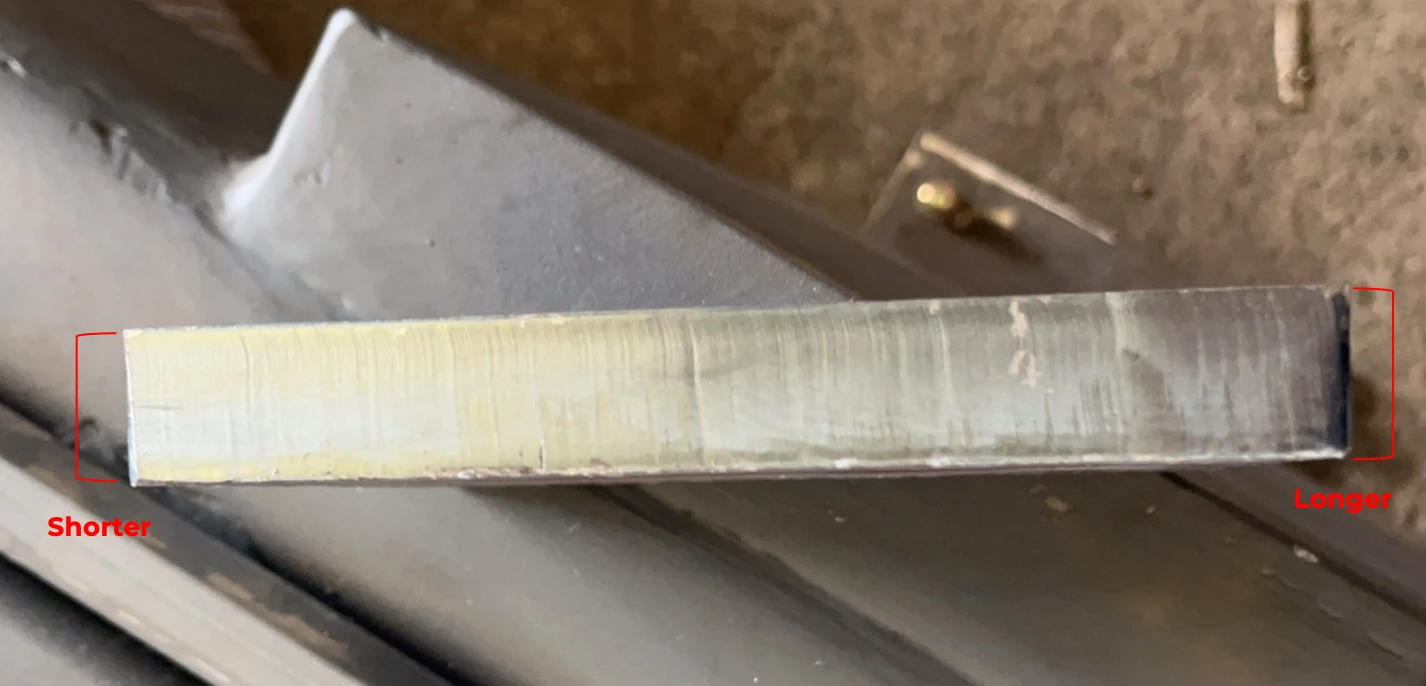
Plasma cutting sample with distinct taper
This is commonly happening because of several factors:
· The cutting speed is crucial, as cutting too slowly can result in a wider kerf, increased heat input, and potential material warping (positive taper). Conversely, cutting too quickly may lead to an incomplete cut, narrower top width, wider bottom width (negative taper), and a rough surface.
· The cutting direction also affects taper, with clockwise cutting producing a positive taper and counterclockwise cutting producing a negative taper.
· Additionally, the condition of consumables in the torch, like the electrode and nozzle, can deteriorate over time, causing the plasma arc to be less focused and increasing taper.
Fiber lasers offer superior beam quality, allowing for a small spot size and narrow kerf, resulting in a clean and straight cut with minimal taper. Their excellent focusing ability further enhances cut quality. These lasers are highly stable, maintaining consistent cutting parameters and preventing taper. Furthermore, fiber lasers have low heat input, especially in pulsed mode, resulting in minimal heat affected zones and reducing taper.
· 3.5 Bevel Cutting
Currently, coastal nations such as South Korea and Japan, heavily committed to maritime transportation development, have seen an increased demand in the shipbuilding and related mechanical industries sectors. These industries rely significantly on beveling cutting technology, underscoring its crucial role in production.
Before high-power lasers became widely used, plasma applied for beveling cutting. However, this method posed several challenges as follows:
1.Careless grinding in the plasma beveling process could result in deep marks, requiring removal if exceeding 3mm. This was critical to ensure proper bevel fusion during welding.
2.Plasma processing, due to its high heat input and a heat-affected zone of around 0.5mm-2.0mm, caused thermal deformation in high-strength steel plates. This called for an additional, laborious deformation correction stage.
3.Programming for the out-dated plasma bevel cutting system requires adjustment for variables such as torch angle, height, kerf width, and speed. This restricts operators from making real-time precision modifications. If changes are needed, it involves returning to the programmer and updating the program, a time-consuming step that hinders the production of high-quality parts.
Utilize high-power lasers, which can shape the bevel in one go, combining multiple stages like cutting and milling. Bodor offers the bevel cutting that the roots of Y, K, and other shaped bevels are uniform and consistent, offering high surface quality.
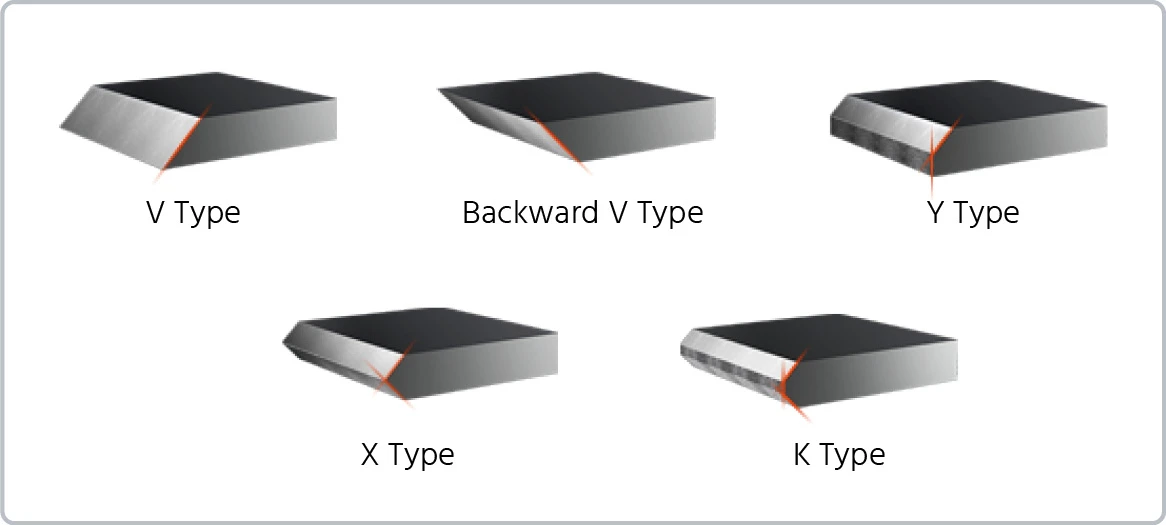
For the application, new ship constructions extensively employ T-shaped components made from high-strength, low-alloy steel, formed using laser processing. This method significantly reduces the ship’s weight and helps design the ship’s flat plates with complex three-dimensional curvatures to meet marine hydrodynamic demands. The laser-assisted method replaces mechanical heating processes, which are laborious, time-consuming, and somewhat risky, and holds great potential for future applications.
· 3.6 Cost Analysis
Unlike traditional cutting methods, laser cutting machines utilize a high-energy laser beam to cut materials without any physical contact, resulting in reduced maintenance costs and longer lifespan for the machine. Additionally, laser cutting machines are highly automated and require minimal involvement from operators, which lowers labor costs and boost productivity. Furthermore, laser cutting machines make the best of materials and consume less energy compared to plasma cutting machines.
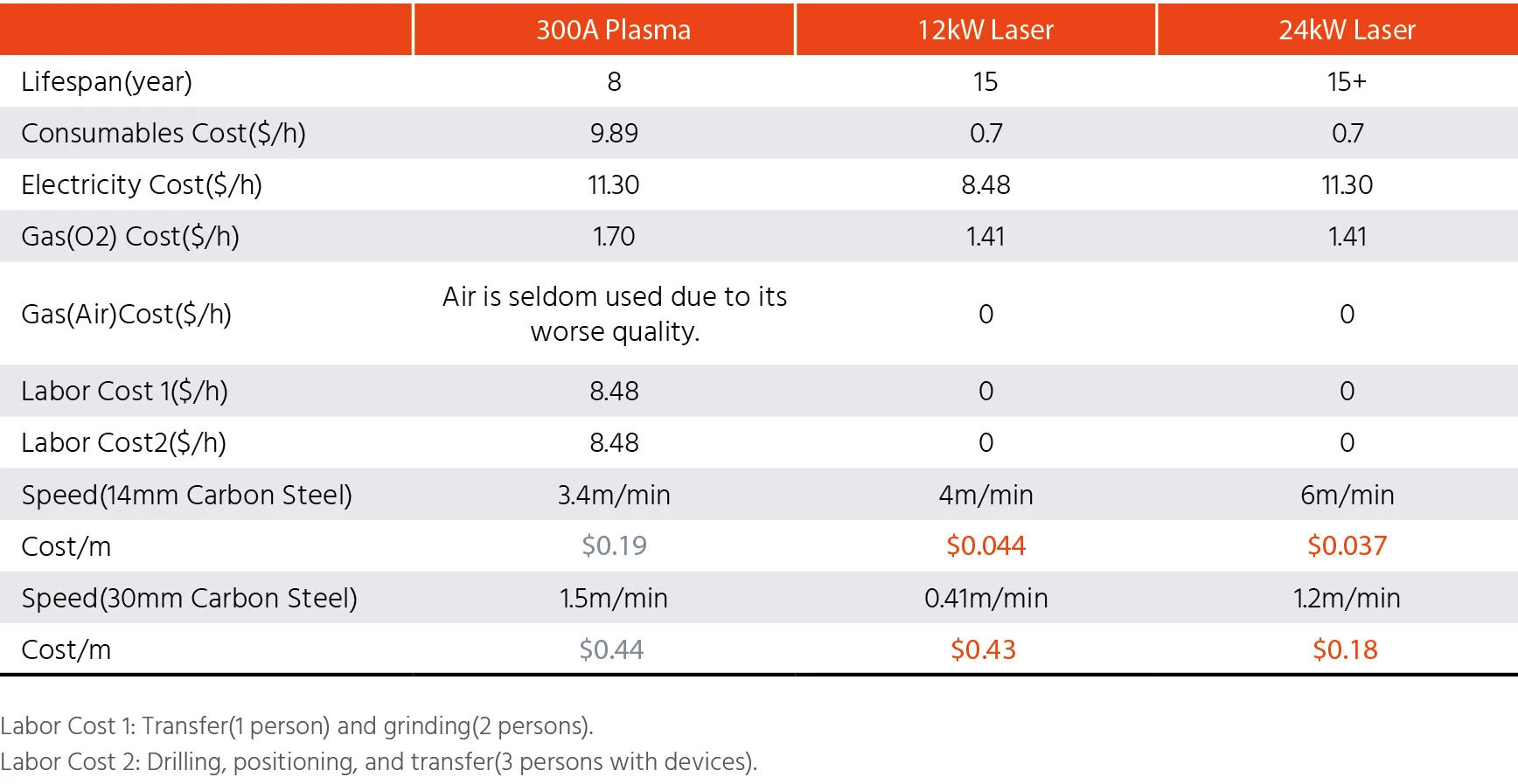
Based on the provided table, it is evident that the operational costs of a plasma cutter over 8 years are twice as high as the operational costs of a 24kW laser cutter over 15 years. The choice seems clear, doesn’t?
· 3.7 Maintenance
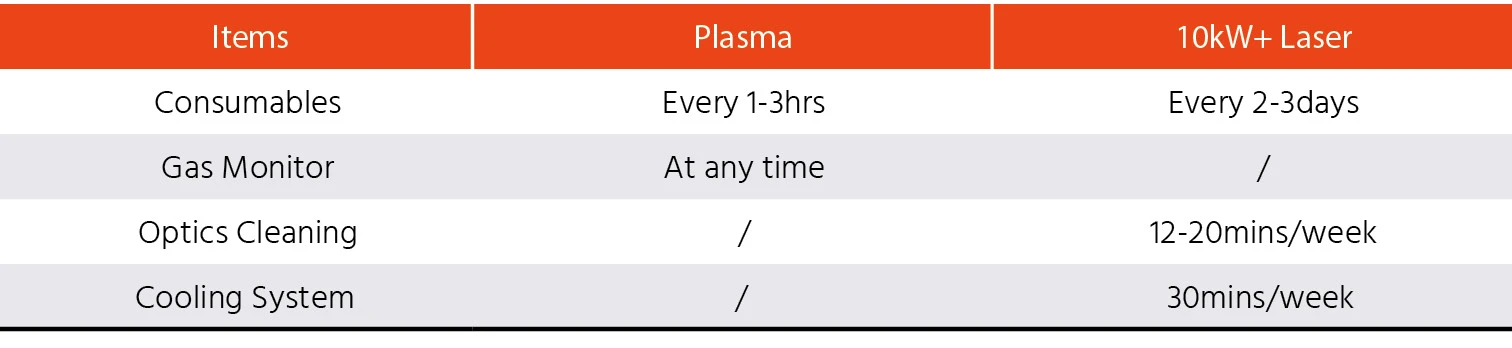
Taking the previous example into account, suppose a company offering metal cutting services that uses plasma for processing 14mm carbon steel. The company might find themselves needing to change consumables roughly every 1-3 hours, and monitor the gas level and pressure from time to time. Contrastingly, with the implementation of Bodor 10kW+ high-power lasers, they could limit their maintenance needs to just 3-4 hours per month.
4.Make the Smart Decision
After reviewing the previous information, you may have a better understanding of the approach your business requires for cutting operations. However, making the final decision can still be a daunting task. The following table may help you make the smart decision that aligns with your business needs and goals.
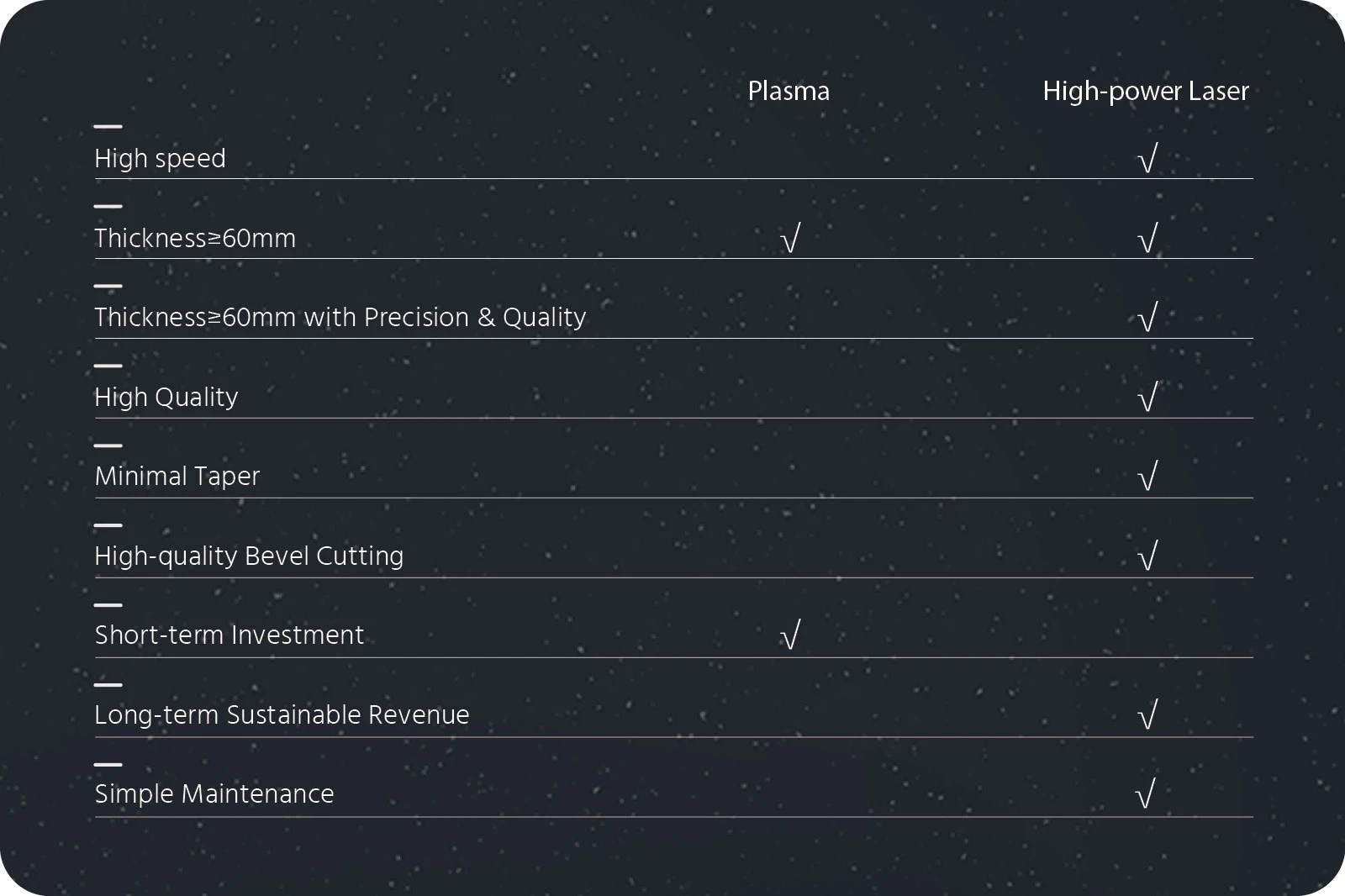
At Bodor Laser, we evaluate your cutting requirements and offer free consultation service on a case-by-case basis. If you require further suggestions, please fill out the form to contact our sales experts.
Leave a comment
Your email address will not be published. Required fields are marked*