Handheld Laser Welding: A Key to Sustainable Manufacturing
A cleaner, more efficient welding solution for the future of manufacturing

Enci
November 25, 2024Trending and helpful laser knowledge for your success
In a world increasingly focused on sustainability, industries are exploring ways to reduce their environmental impact while improving efficiency. Laser welding stands out as a transformative technology that aligns perfectly with these goals. Among its many innovations, the handheld laser welder is making significant strides, offering a portable and versatile solution for eco-conscious manufacturing. This blog explores the environmental advantages of laser welding and highlights the growing role of handheld laser welders.
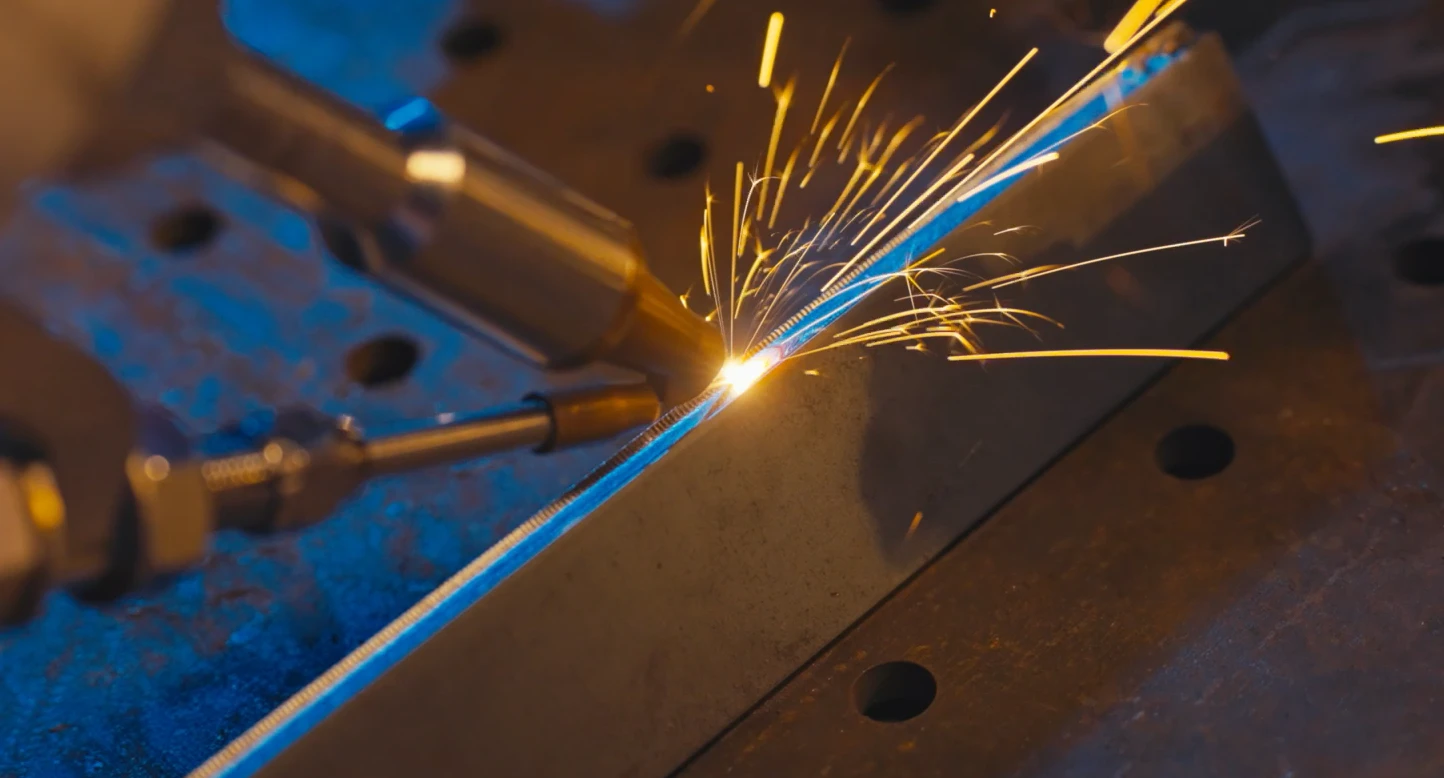
The Environmental Drawbacks of Traditional Welding Methods
Traditional welding methods, such as Manual Metal Arc Welding (MMAW) or TIG/MIG welding, are associated with significant environmental challenges:
High Energy Consumption:
Traditional welding processes dissipate amounts of heat into surrounding areas, leading to energy loss rather than focusing the energy on the welding zone. They also typically require more time to complete a weld due to slower deposition rates resulting in prolonged energy usage.
Material Waste:
The use of filler materials, coated electrodes, and fluxes is typically higher than necessary, leading to overuse and wastage. Additionally, spatter, splatter, and leftover materials from imprecise welds contribute to resource inefficiency.
Pollutant Emissions:
Conventional welding methods release pollutants, such as gases and particulates from coatings and fluxes, further damaging the environment. Additional drawbacks include high heat input, welding splatter, and thermal distortion, which require energy-intensive corrections.
Traditional welding method poses serious health risks to operators:
Harmful Emissions:
High heat input from conventional welding melts and vaporizes base metals, filler metals, and coatings, releasing gases and particulates. These include nitrogen oxide, carbon monoxide, and ozone, which contribute to harmful welding fumes.
Long-Term Health Risks:
Prolonged exposure to welding fumes can lead to respiratory illnesses, skin irritation, and even more severe conditions such as lung disease.
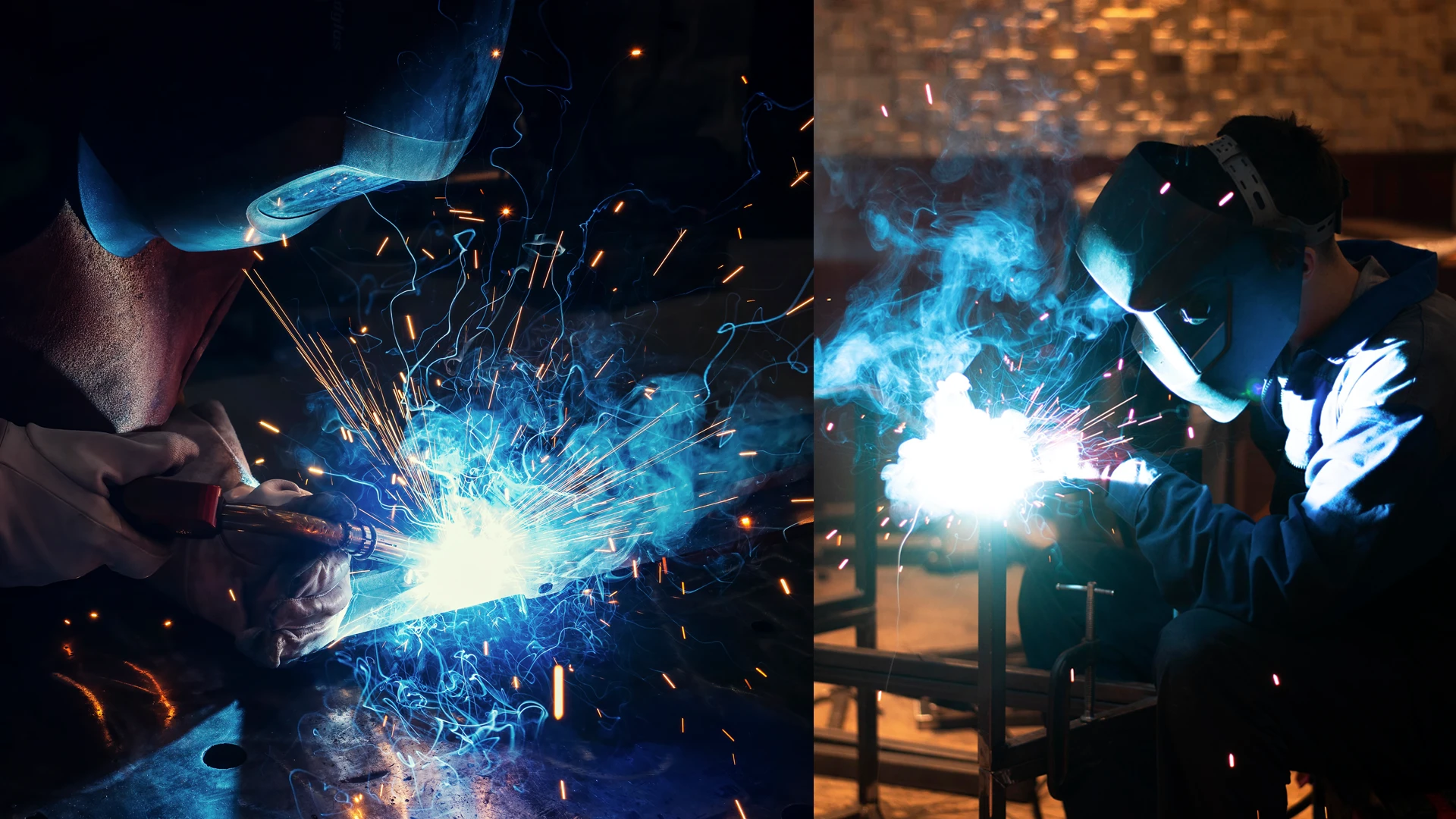
fumes produced by traditional welding
Laser Welding: A Safer Alternative
Laser welding offers a cutting-edge solution to these challenges, combining precision, efficiency, and safety:
Reduced Emissions:
By using a highly focused beam, laser welding minimizes the vaporization of materials, significantly reducing the release of harmful gases and particulates.
Lower Heat Input:
The precision of laser welding ensures that only the necessary area is heated, avoiding unnecessary melting of base or filler metals. This reduces fumes and prevents heat-related damage to surrounding materials.
Healthier Work Environment:
Laser welding operates with less noise and vibration, improving the overall safety and comfort of operators. Additionally, the reduced reliance on fluxes and coatings further minimizes health hazards.
Handheld laser welding combines the precision and power of traditional laser systems with portability and ease of use. Designed for both on-site and workshop applications, handheld laser welders bring unmatched versatility to a variety of industries.
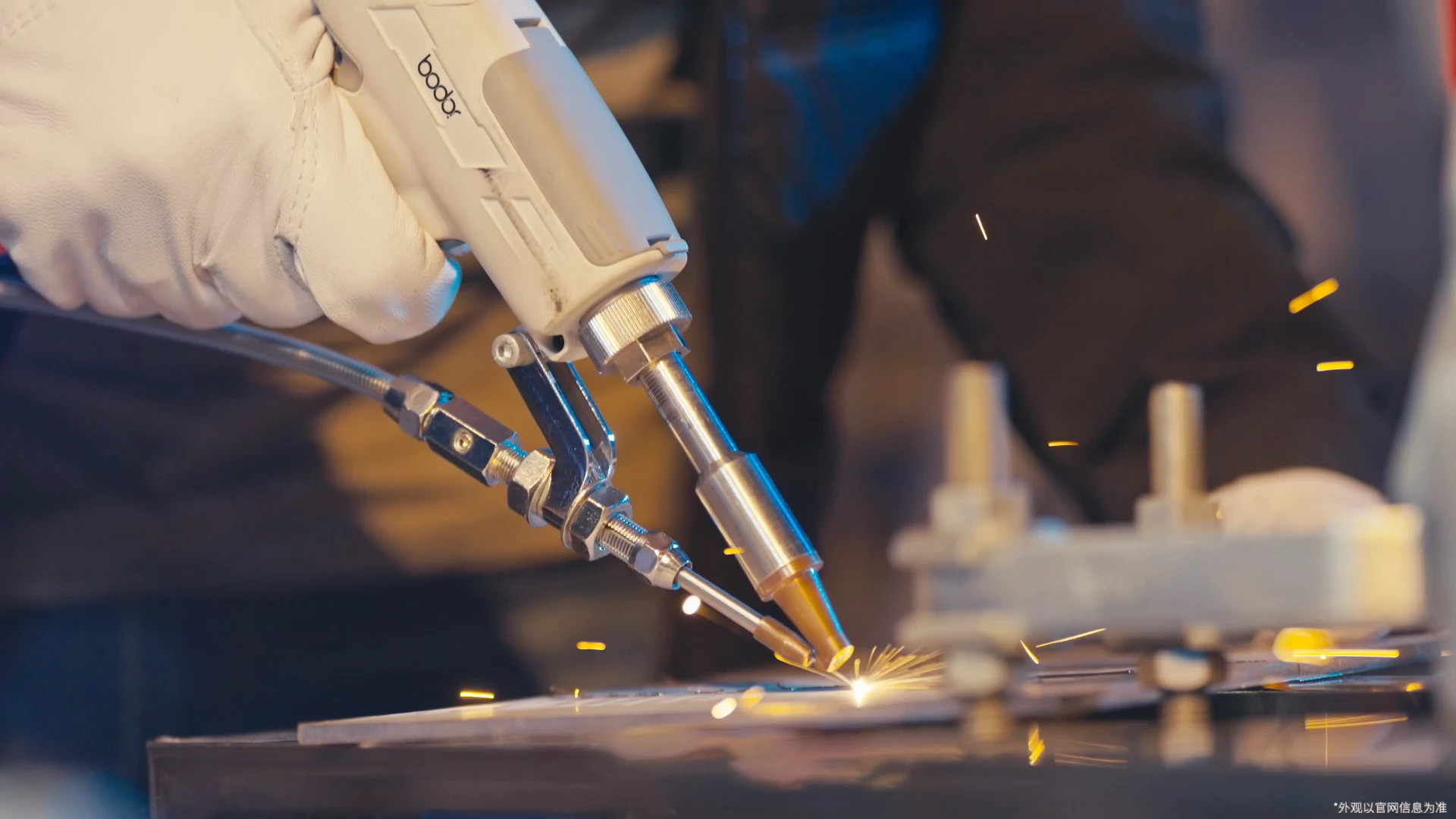
Can Handheld Laser Welders Help My Industry?
Absolutely! Handheld laser welders are revolutionizing following but no limited industries by providing an eco-friendly, cost-effective, and flexible solution:
Kitchenware Manufacturing: Ideal for creating seamless joints in stainless steel kitchenware, ensuring both strength and aesthetic appeal.
Sheet Metal Processing: Delivers precision for cutting and welding metal sheets used in various industrial applications, reducing waste and enhancing productivity.
Stainless Steel Products: Perfect for crafting durable and visually appealing stainless steel items such as countertops, sinks, and decorative pieces.
Crafts and Artistic Designs: Offers exceptional precision for creating intricate patterns and artistic metal crafts with clean, smooth edges.
Furniture and Appliances: Ideal for welding metal frames, decorative finishes, and structural components in modern furniture and home appliances.
Whether you’re in manufacturing, maintenance, or repair, handheld laser welders can streamline your operations while supporting your sustainability goals.

If you’re looking for the best in handheld laser welding, don’t waste time searching for “handheld laser welder near me.” Instead, consider Bodor’s industry-leading solutions:
Bodor Air1200 Handheld Laser Welder
Bodor Pro1500 Handheld Laser Welder
Both handheld laser welders models are designed to reduce material waste, lower energy consumption, and offer cleaner, safer working conditions—perfect for industries embracing sustainability. Here’s how you’ll benefit:
Continuous Laser Output for High Efficiency
Bodor welders provide a continuous laser output, improving work efficiency and delivering stronger, high-quality welds.
Wide Operating Temperature Range
With an operating temperature of -20°C to 40°C, Bodor handheld laser welders are suitable for a wide range of environments, whether in winter’s cold or summer’s heat.
User-Friendly One-Click Operation
No welding certification is needed! With just 30 minutes of training, even beginners can achieve results equivalent to those of experienced welders.
Wide Voltage Compatibility
Designed for 100V-240V voltage ranges, Bodor welders can be used in various regions. They are also equipped to handle voltage fluctuations, ensuring consistent welding performance without interruptions.
Energy Savings with Lower Operating Costs
Compared to water-cooled handheld laser welders, Bodor’s systems consume nearly 50% less energy. This not only lowers electricity costs but also makes them far more energy-efficient than traditional welding methods.
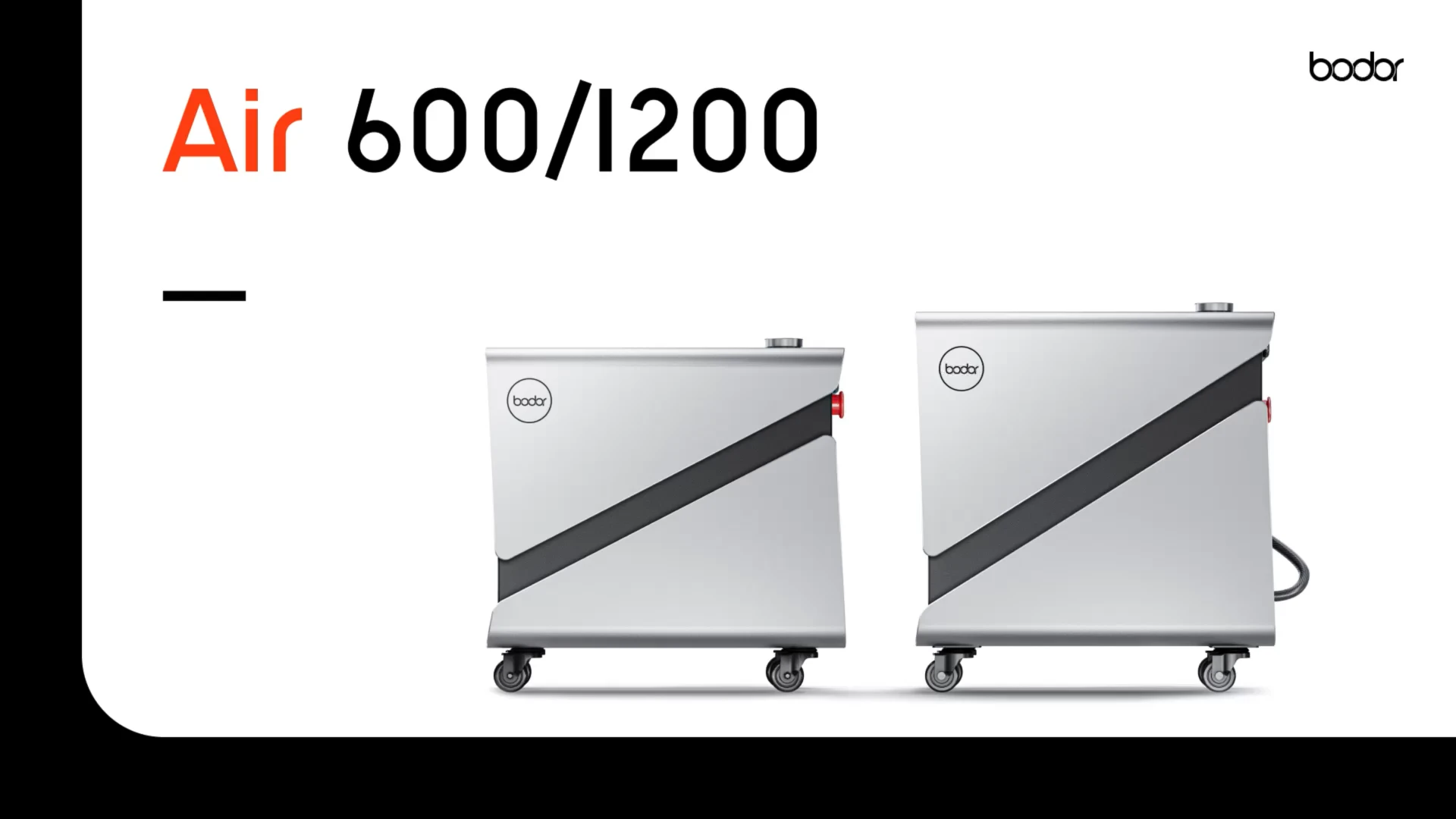
Conclusion
Handheld laser welders represent a remarkable advancement in sustainable manufacturing, combining precision, efficiency, and safety in a compact and portable package. Compared to traditional welding methods, they offer significant environmental advantages. With innovations like Bodor’s Air1200 and Pro1500 models, industries can improve their operations while achieving their sustainability goals. These devices empower businesses to adopt eco-friendly practices without compromising productivity or quality. Whether you’re in automotive, construction, electronics, or aerospace, handheld laser welders are the future of efficient, green manufacturing. Contact Us to explore how Bodor handheld laser welders can transform your processes and lead your industry toward a sustainable future.
Leave a comment
Your email address will not be published. Required fields are marked*